Quality Policy
- Home
- Quality Policy
Quality Control
DAS adheres to a rigorous quality control discipline throughout its activities.
Quality Plan Narrative
• The Project Engineer is responsible for preparing the Project Quality Plan during mobilization.
• Reviews and updates take place within each three month period.
• Initial and subsequent issues of the Project Quality Plan undergo review and approval by the General Manager.
Procedures For Improved Process
• DAS has developed manual procedures for quality control activities.
• Emphasis is placed on continuous improvement and instilling customer confidence by the General Manager.
Communication of Technical Requirements
Technical requirements of contract are communicated to personnel through:
• Selective issuance of the specification and drawings.
• Selective issuance of the project quality plan.
• Frequent staff meetings and briefings, especially for technically demanding operations.
Integrations Of Client Specifications
• The technical requirements of the client, as defined in the specification, are integrated into the Quality System.
• Client specifications take precedence over corporate standards, as determined by the General Manager.
Quality Control Plans
• QCPs are prepared for activities specified in the contract or where management deems quality would be adversely affected by the lack of control.
• QCPs extend to relevant subcontractor activities, ensuring testing and monitoring through witness and inspection.
On-Site Quality Control
• The project team expedites quality control on-site using Performa documentation.
• Performa documents the salient verifications and hold points, ensuring comprehensive quality oversight.
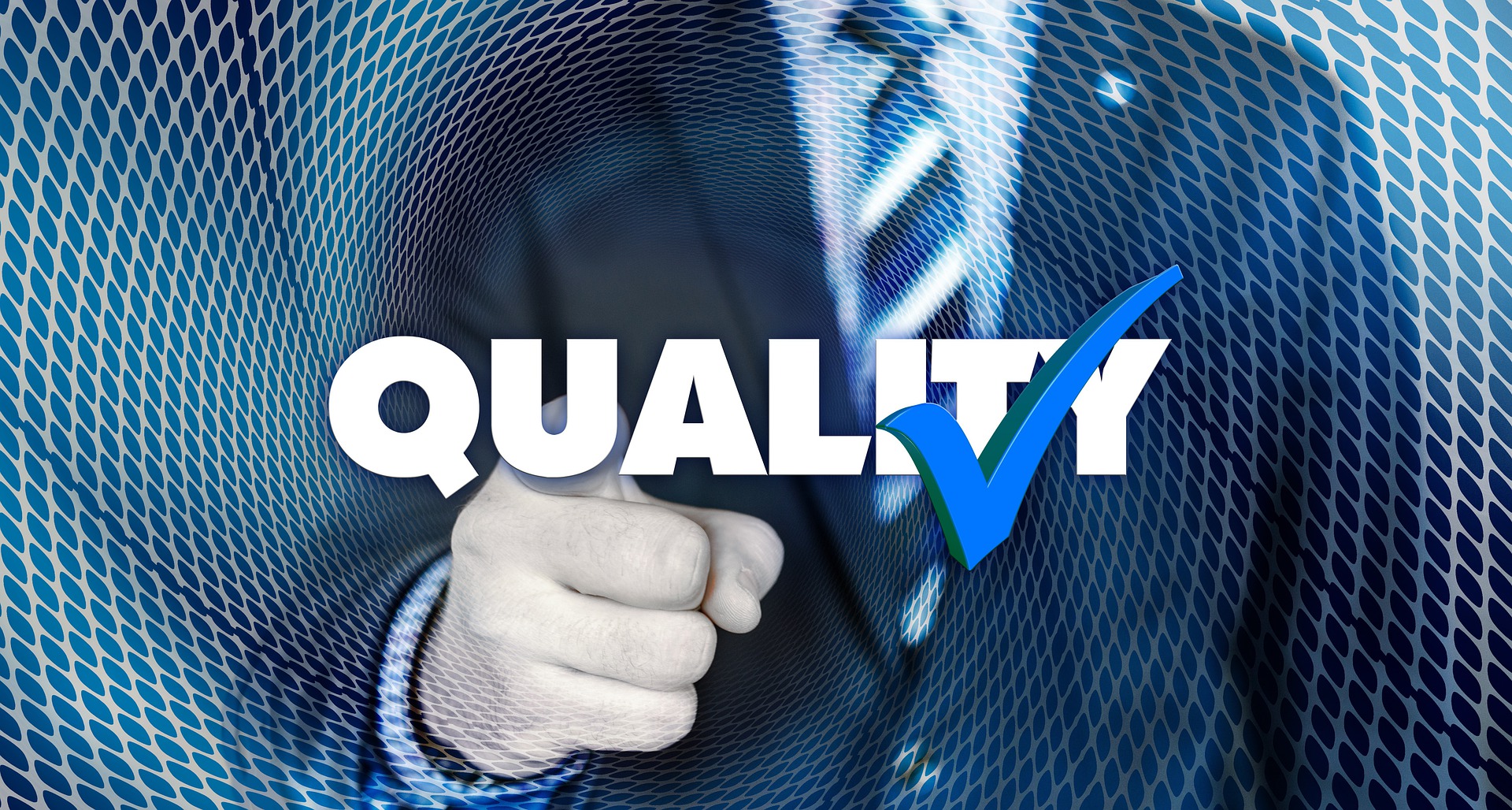